The Critical Role of Sterility Testing in 503B Compounding Facilities
A 503B compounding facility, also known as an outsourcing facility, is a type of pharmaceutical compounding business that operates under section 503B of the Federal Food, Drug, and Cosmetic (FD&C) Act. The concept of a 503B pharmacy was introduced with the passage of the Drug Quality and Security Act (DQSA) in 2013. These facilities can manufacture bulk pharmaceuticals and are the only pharmacies permitted to provide compounded medications in bulk for use in physicians' offices, clinics, and hospitals. Because many of these facilities compound sterile drugs such as injectables, intravenous, and intraocular formulations, sterility testing is a critical regulatory compliance requirement. It is essential to minimize patient harm resulting from potential microbial contamination.
When is sterility testing required?
The FDA requires 503B outsourcing facilities to perform sterility testing for all drugs reported as sterile, with additional separate endotoxin testing required for non-pyrogenic products.
How is sterility testing performed?
Membrane Filtration
The first method is membrane filtration, preferred if the tested drug product is filterable, as defined in USP <797> and USP <71>. This technique involves filtering a test sample through a membrane filter that retains microorganisms that may be present. The filter is then rinsed and incubated in a growth medium to detect the presence of any viable microorganisms. Membrane filtration can be done in an 'open' or 'closed' format.
Open Membrane Filtration
The "open" format involves passing the drug product through an open funnel containing a filter. Once appropriate filter rinsing is complete, the filter is removed, cut in half, and placed into tryptic soy broth and fluid thioglycollate medium. Incubation then occurs at the appropriate temperatures and duration. While the setup is simple and less expensive than closed systems, the required handling of the filters can increase the risk of human error, and the open nature of the setup may increase the risk of contamination during the test procedure.

Closed Membrane Filtration
High-risk or critical applications generally favor “closed” systems as they reduce the risk of test faults by housing the membrane filter within a sealed system, protecting it from environmental exposure and handling errors. Avoiding test faults is crucial as they can lead to false positives, unusable products, or delayed drug release. While closed systems can be more expensive and complex, they minimize the risk of external contamination and provides better assurance of maintaining sterility throughout the process.

Featured Membrane Filtration Products
Direct Inoculation
The second method is direct inoculation, which involves directly injecting the drug product into growth media to detect for both aerobic and anaerobic microorganisms. This method provides a simple mode for sterility testing of materials that cannot be easily filtered or have a small sample volume.

Featured Direct Inoculation Products
Free Resources
Sterility testing in sterile compounding is integral to routine quality control and crucial to ensuring that compounded sterile drug products are free from harmful microbial contamination. It safeguards public health and reinforces the credibility and reliability of 503B facilities in the healthcare industry. Hardy Diagnostics understands the unique needs of those working in critical environments. Visit our Sterility Testing product suite or download our catalog for more information.
References:
United States Pharmacopeia Chapter <71>
United States Pharmacopeia Chapter <797>
FDA Current Good Manufacturing Practice—Guidance for Human Drug Compounding Outsourcing Facilities Under Section 503B of the FD&C Act Guidance for Industry

Meet the author
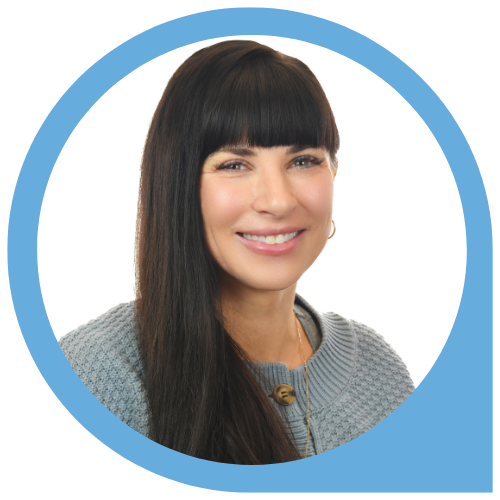
PHARMACEUTICAL PRODUCT MANAGER at HARDY DIAGNOSTICS
Joelle Brackeen, B.S. Marketing
Joelle Brackeen is the Pharmaceutical Product Manager at Hardy Diagnostics and has over a decade of experience in Marketing and Product Management. Before transitioning to the pharma sector, Joelle had the privilege of co-founding and helping to grow a business into a highly profitable, multinational enterprise. Her unique blend of entrepreneurial spirit and product management expertise contributes to her innovative approach and ability to drive successful products and strategic initiatives in the pharmaceutical industry. In her free time, she enjoys playing the piano and spending time at the beach.